Open Your World
The trusted international elogistics partner, powering your ecommerce growth
Our International Logistics Solutions
Parcel delivery made easy with International Logistics Services
At Landmark Global, we are experts in international logistics services: transporting, clearing, and delivering e-commerce products directly to customers all over the world.
500 + leading e-commerce customers
75 commercial partners
25 facilities across 4 continents
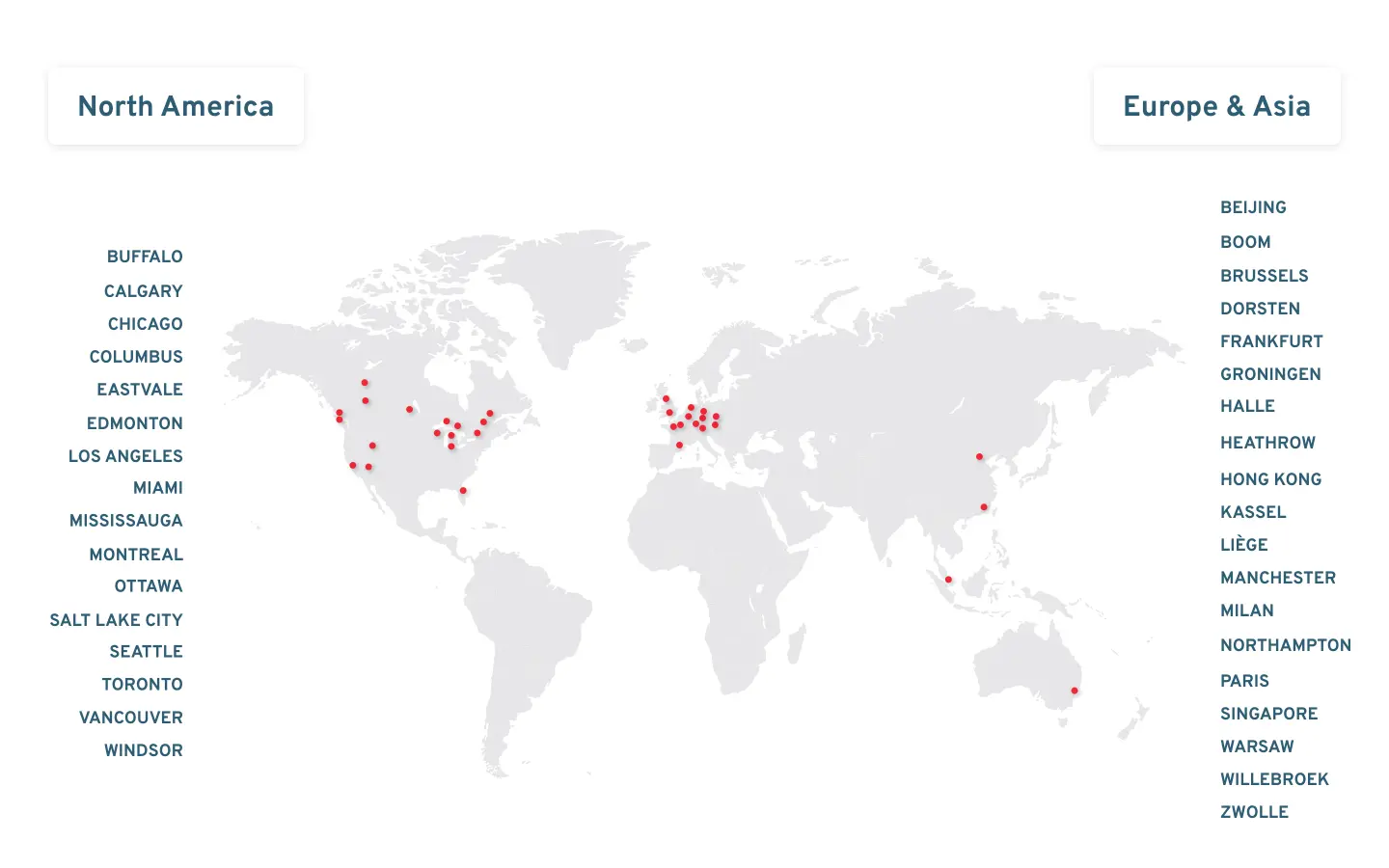
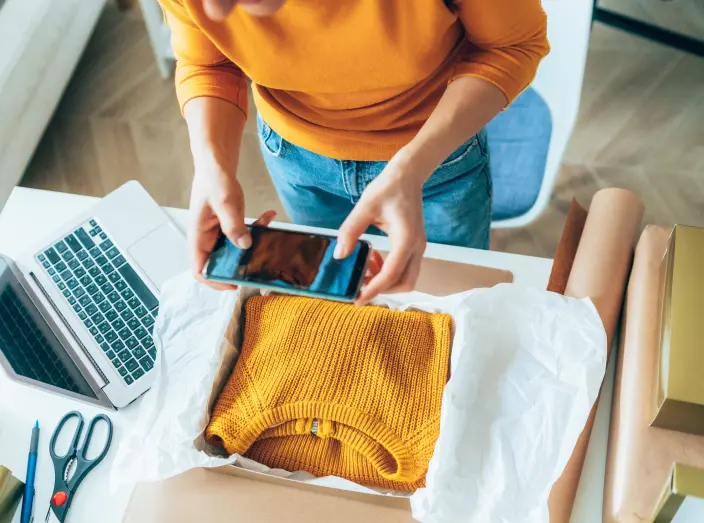
Flexible returns management
We make returns management as smooth and simple as possible, with a range of flexible solutions depending on your destination, speed and size of parcel.
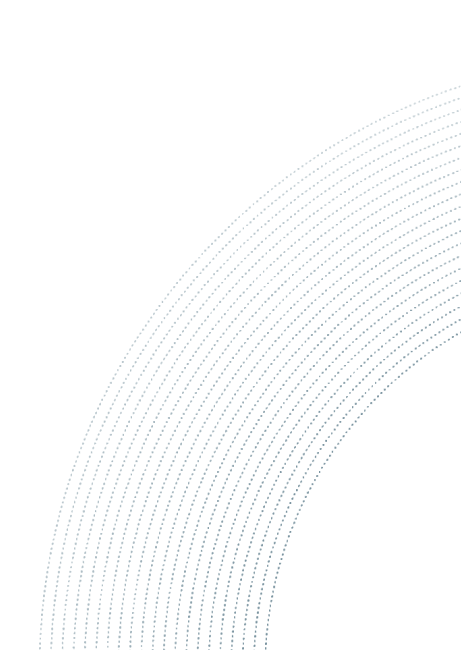
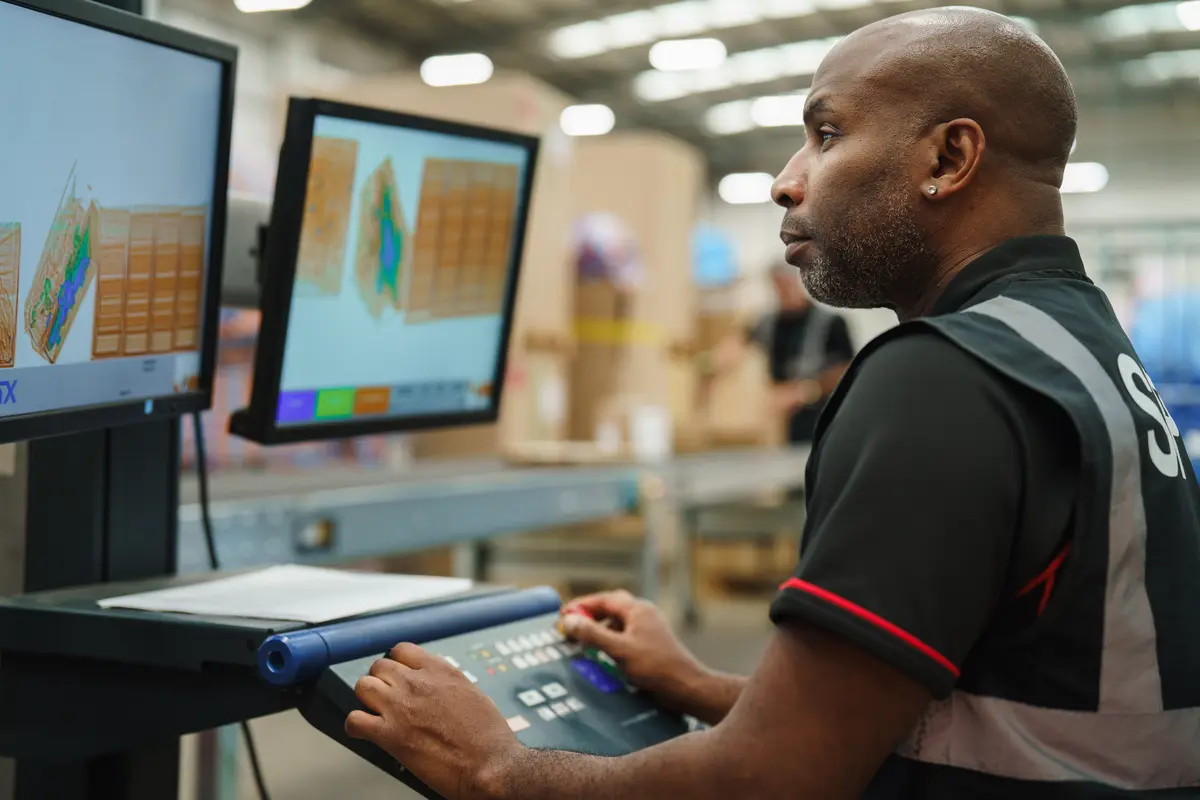
Customs Clearance
We combine in-house compliance expertise with a local presence in key e-commerce markets to ensure your shipments are processed efficiently with our customs clearance services.
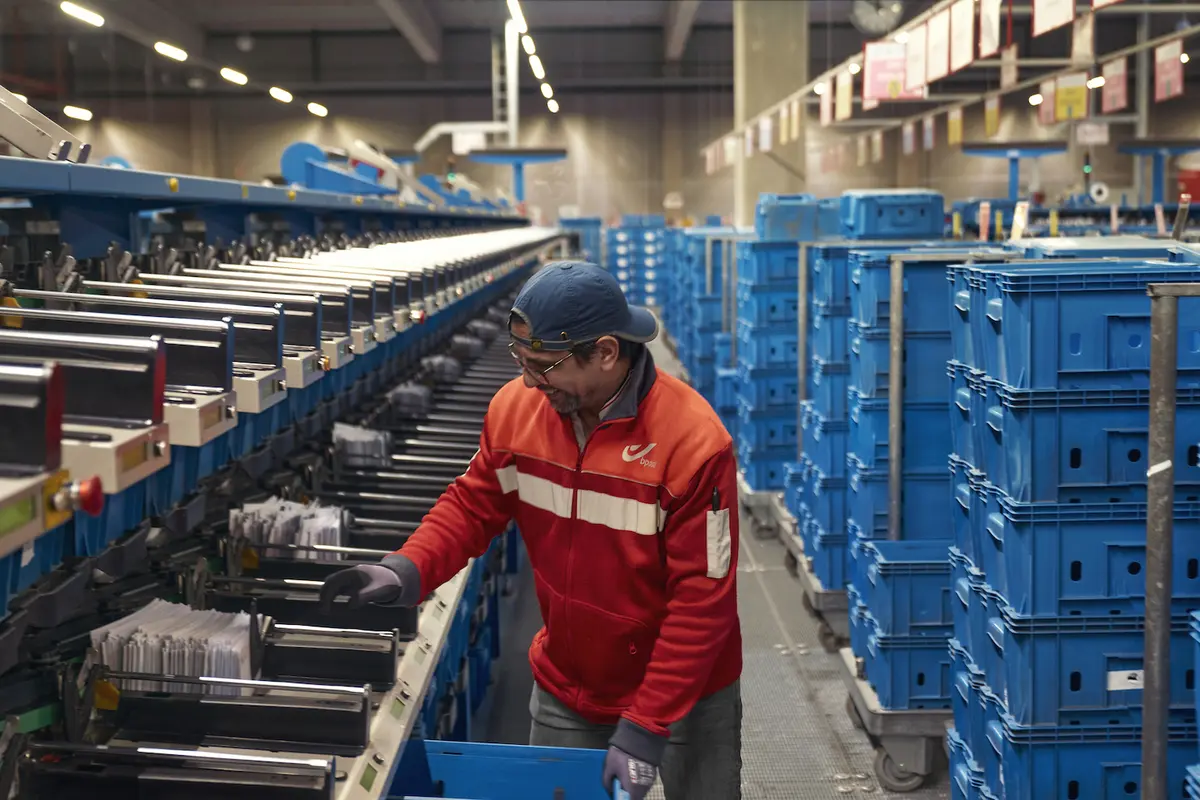
International mail delivery
We provide you with extensive knowledge and experience in mail delivery globally with daily connections to postal operators worldwide.
“The onboarding process was simple and straightforward. The ongoing support from the Landmark Global teams is excellent.” - Jack Sandford, founder of One Choice Apparel
Trusted by leading e-commerce companies including
Landmark Global Logistics Services
Your trusted international logistics partner, providing top-notch parcel services and stimulating e-commerce growth.
Logistics Company with Years of Experience
At Landmark Global, we have been dealing with cross-border delivery for years. Thanks to the experience that we had gathered over time, we were able to master the art of delivery. Our logistics services for companies are impenetrable and resistant to any disruptions due to our highly vetted procedures. We have managed to build the crucial infrastructure in over 220 destinations in the world, making deliveries easy and quick for our clients.
Parcel Delivery Service Tailored to Your Need
Whether you need an e-commerce logistics solution or services adjusted to the specifics of a large corporation, we are here to help. We put your business, no matter small or big, in the centre and provide you with package delivery that is as customised to suit your needs as possible. Take a look at a full list of our services, contact us, and discover how we can help you take your business to the next level.
More Than Just International Parcel Services
We use our knowledge to help businesses from all over the world in more than pure parcel delivery. Our customs clearance services help you comply with the laws and regulations of your destination, while we also offer returns management and a range of services tailored to the needs of e-commerce stores.
We also share our knowledge with you, helping your business grow in the world of cross-border commerce. Our experts are at your disposal, and our customer service agents are there to help solve your problems, answer your questions and adjust our parcel delivery to meet your needs. We are there for you.
Parcel Delivery Company Appreciated by Many
Our expertise has been recognised and appreciated by over 500 e-commerce clients and 75 partners working with us worldwide. We have proven to them that we are a reliable, high-quality international delivery company, so we are ready to prove it to you. Let our clients’ satisfaction be our review – one that points out our excellence, attention to detail and dependability.
Landmark Global – Your Trusted Partner Worldwide
With 25 logistics centres on 4 continents, we shall become your best logistics partner – a company that you can trust with even the most precious, business-sensitive parcels. So, contact us now and learn how we can help you expand your business to foreign markets!
News & Insights
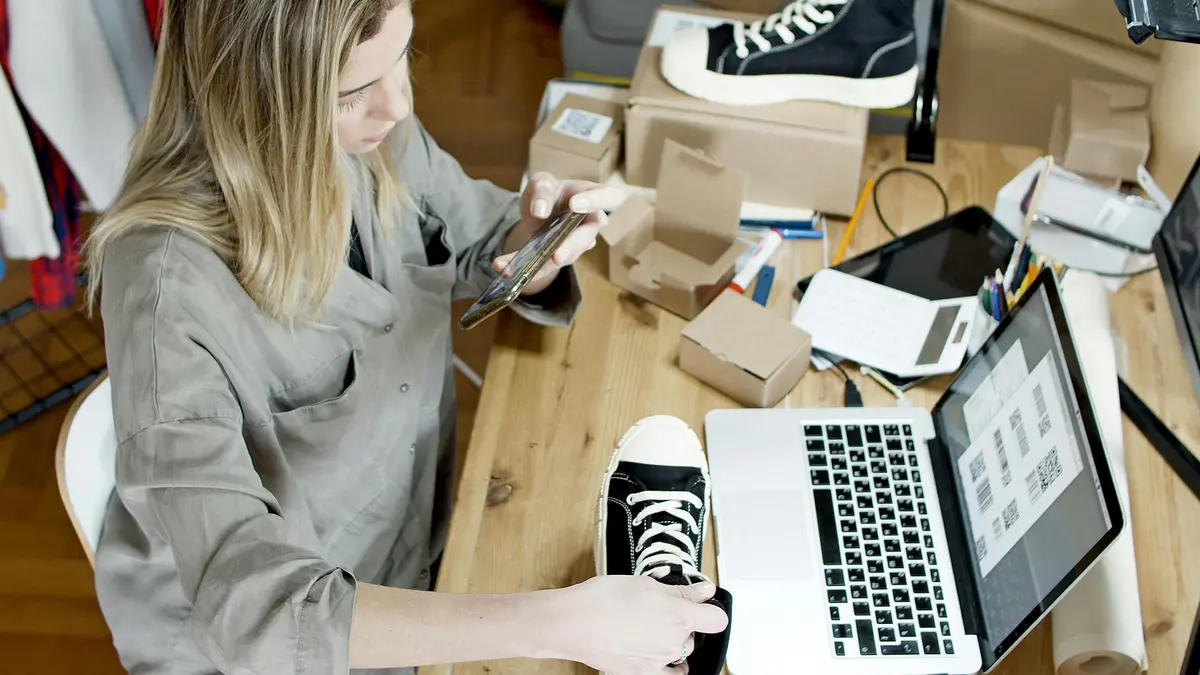
High Pressure on Reverse Logistics: Why Fashion Retailers Brace for Impact in July
Returns in fashion e-commerce spike sharply in July, driving up costs and operational pressure. Discover how fashion retailers are adapting to seasonal surges with smarter returns tech, local consolidation, and new sustainability strategies, all while facing return rates of up to 60% and €15 per parcel.
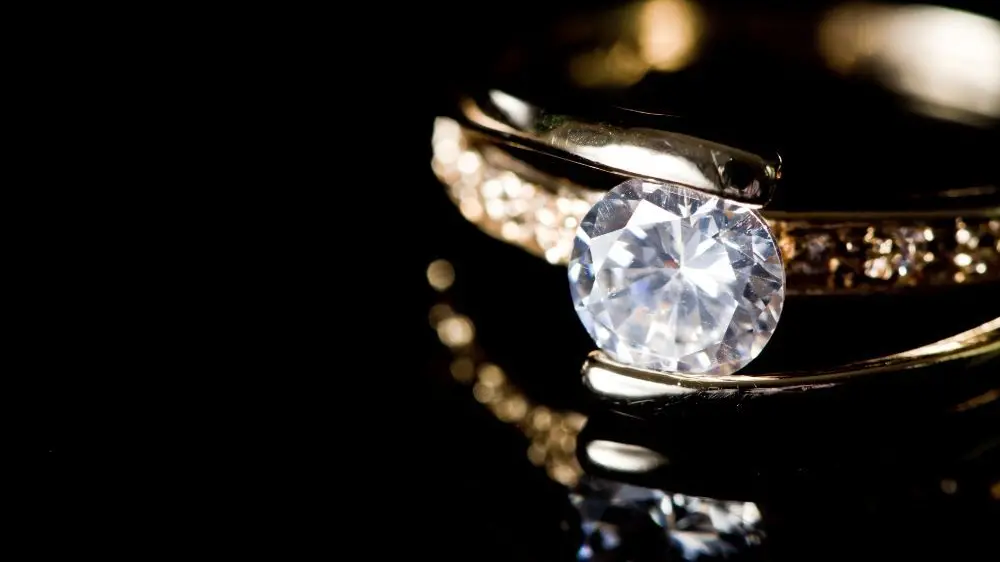
Luxury Industry Logistics: Navigating July's Challenges in E-Commerce
The luxury e-commerce industry is booming, set to grow from $20.43B in 2024 to $33.03B by 2029 (CAGR 10.12%). But July's discount season brings challenges—from rising return rates to logistical pressure. Learn how top luxury brands navigate sales without compromising brand value.
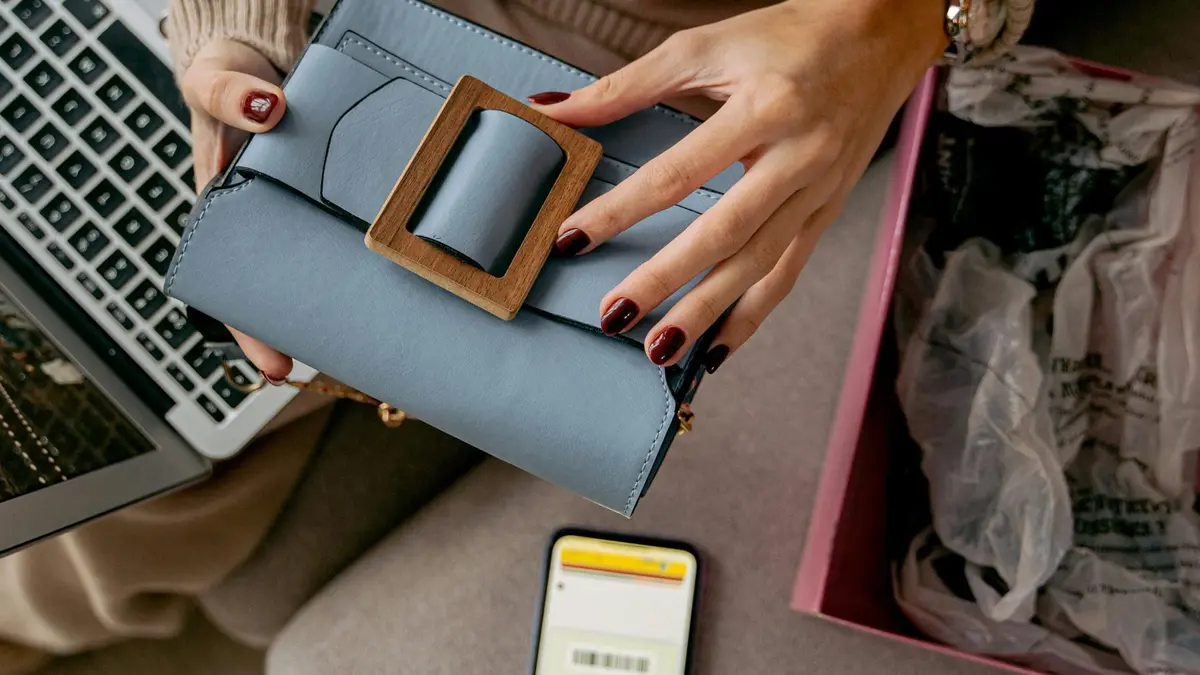
Why Your Returns Strategy Matters More Than Ever
With summer sales just kicking off, returns are about to spike, making now the perfect time to rethink your returns strategy. In this timely article, Landmark Global's Product Manager Anastasia Heaslewood explores why returns are no longer a back-office issue but a front-line experience that can win or lose customers.